2.Safety in specialized fields
2-1 Experiment Safely
2-1-1 Staying Alert to Danger
At our university, as a general rule, it is prohibited to do dangerous experiments alone at night. Please thoroughly understand the characteristics, purpose, and procedures for each experiment, and the performance function of equipment used, properties of materials and chemicals, and meet with the supervising teacher, to prepare a test plan before carrying out experiments. Absolutely do not leave equipment or materials unattended during experiments or work under dangerous conditions where accidents cannot be prevented. Otherwise dangerous incidents or conditions may be overlooked and there is a risk of causing serious problems. Eating and drinking are prohibited from a safety standpoint in laboratories handling substances with high toxicity and flammability.- Do not forget that there is always the possibility of danger involved with any experiment.
- Unfamiliar or dangerous experiments should be avoided during nighttime, and should never be done alone.
- Should you discover a problem with a device etc, immediately stop the experiment and report it to your supervisor.
- Be on the alert for the smell of gas or abnormal machine noise.
- Read the instruction manuals for experimental equipment / devices. Follow standard practice and get used using to the required devices and materials.
- Do not work when you are not alert. Also, do not use devices or materials with which you are unfamiliar.
- Do not eat, drink or smoke during experiments (all indoors areas are non-smoking).
- Be familiar with the location and use of safety equipment so that you can always respond to emergency situations.
- After experiments, return remaining chemicals and materials to the specified storage place, and be sure that experiment waste liquid (including waste water) is stored or discarded according to the rules.
2-1-2 Clothes and Footwear
Wear work clothes and white coats that are easy to move and work safely in. Footwear should be slip resistant and stable on your feet. Wearing shoes with high heels is banned as it may cause stumbling.When there is a danger of heavy objects falling on your feet, wear safety shoes with a steel lining. When handling chemicals, dry ice, and high temperature objects, use protective gloves suitable for each substance and job.
- In the case of work where there is danger of fire, wear natural fabrics rather than artificial fabrics.
- For chemical experiments, use long sleeve white gloves and aprons to protect the body from corrosive substances .
- If necessary, use a hat or a helmet to protect the head.
- Do not wear dangling accessories, such a ties, that can be caught in rotating equipment.
- Secure long hair in buns so it will not get caught in machines or burn.
- Always use safety glasses or goggles to protect your eyes.
- Wear appropriate masks for dust and fumes.
2-1-3 Safe Working Posture
Maintaining the same posture for a long time causes static muscle fatigue. Light gymnastics are effective for solving this problem. Stand or sit up straight near equipment and desks and try to work in a natural posture.- Avoid work in narrow places as much as possible.
- When passing behind a dangerous work area or an experimenter, pay attention to surroundings and announce your presence.
2-1-4 Tidiness / Organization / Cleanliness / Cleaning / Inspection
The basic principles of safety are order, organization, cleanliness, cleaning, and inspection at the start of business. If there is nothing on the floor, one cannot stumble, If you maintain an organized and tidy room safety will be improved.- Treat your laboratory like your own home, keeping it clean and tidy.
- Do not put anything near a gateway, emergency exit, stairway or entrance.
- Establish a place to put each object, always making sure to return it to the predetermined position after use.
- Always. clean up desks and tables after each use.
- When leaving your work desk/table, push the chair under the desk/table.
- fire extinguishers in a visible location where they can be easily taken out for use.
2-1-5 Water Accidents
Faucet and hose connections are where many troubles occur. Many kinds of equipment and instruments become unusable when inundated with water, and if notes and books get wet, it can hinder research.- When the laboratory is unoccupied for a long period of time, as a rule, do not leave the water running (close the faucet). When water needs to be running, secure the faucet or appliance with wire to prevent the connection to the hose from ever coming loose.
- Perform an inspection of hose connection points for signs of deterioration once a month.
- If a water leakage occurs, close the main water supply valve, stop the equipment, report it, and investigate and remedy the problem or damage.
- If an outlet or electric cord gets wet or water comes into contact with electrical equipment, avoid electric shocks in the affected wet area.
2-2 Electricity
2-2-1 Basic Precautions for Using Electrical Equipment
In addition to the power supply (single phase AC 100 V and 200 V) used for general equipment, there are three-phase AC 200 V power supply laboratories, which are used for large motors and compressors etc. that require high electric power. Below, we will explain the precautions for handling this electrical equipment.- Make sure that electrical appliances are functioning normally before use.
- Connect only to outlets with the voltage appropriate for the rating of the equipment, using a cord with sufficient current capacity.
- Plug, and unplug cords by gripping the plug.
- In principle, electrical equipment should be connected to an earth ground.
- Do not exceed maximam capacity of power strips by connecting too many devices.
- Do not place heavy objects on electrical cords. Also, do not place cords where people can trip over them.
- Take care not to cause poor contact or a short circuit at the plug and cord connection.
- Be careful to not let dust and water come into contact with plug connections. This can cause electric leakage that generates heat, which may cause fire.
- Before examining the inside of electric appliances or repairing, be sure to unplug from the outlet.
- When not using equipment for a long time, remove the plug from the outlet.
2-2-2 Electric Shock
Please be careful to avoid secondary shocks in the case of electric shock accidents. For example, you may fall when shocked, hit your head, or fall down from a high place. To prevent electric shock accidents, pay attention to the following.- Ensure that the wiring between all the devices is inspected and that there are no bad connections.
- Do not touch electrical equipment with wet hands. Also, do not place water on or around electrical appliances.
- In high-voltage equipment experiments, pay careful attention to usage. Operating such equipment by oneself is dangerous. Establish a way to communicate danger to your workgroup, being sure to turn on and off the power after signaling each other.
- If an electric shock accident occurs, immediately undertake a rescue after turning off the power. When it is unavoidable to touch live electric wires and electric devices during rescue, use dry wood, bamboo sticks, rubber gloves etc, instead of your bare hands.
2-2-3 Electric Disaster
Electrical accidents can include electric shocks, fire, explosions, etc. Since there is a possibility that both can lead to serious injuries, it is necessary to pay sufficient attention to experiments using electric current and electric equipment.- Turn on and off the power after checking the safety of the operation of the equipment. Also, in order to prevent electric shock accidents, don’t turn equipment on or off before clearly signaling or informing the equipment operator. It is extremely dangerous to suddenly energize equipment without first doing this.
- Electric heaters, soldering irons etc. can easily cause fires. Forgetting this is extremely dangerous. In addition, burns may be caused by residual heat after equipment use, or flammable substances may ignite.
- Do not place combustible materials such as organic solvents near switchboards, outlets, and electrical equipment. Sparks during the interruption of electricity may cause explosion or fire. In addition, refrigerators have a switch for temperature control, but if explosive gas leaks into the cabinet, it may explode from sparks when the switch is operating, so be careful.
2-2-4 Response to Power Failures
- When a power failure occurs, be sure to switch off at the time of statutory electrical inspection (remove plug).
- If you leave equipment switched on at the time of a power outage, and the equipment starts to move when energized, this can cause a big accident or breakdown.
2-3 Machines
2-3-1 General Precautions
Safe machine operation starts with dressing in proper clothes, protective shoes, and long hair ties. Wear clothes that cannot be caught in the machinery without gloves. Always wear protective eyewear and mask. Doing daily regular inspections prevents accidents.2-3-2 Precautions for Machine Tool Operation
- Receive guidance from the responsible person and use the machine tools with a good understanding of usage and possible dangers.
- Do not operate unfamiliar machines.
- Do not place anything on or near the machines.
- Confirm that the machine is safe to use, including attached cutting blades etc.
- As a general rule, each machine should be operated by one person.
- If any abnormality occurs while using a machine, immediately stop the machine and contact the person in charge.
- Machines and tools must be cleaned including the surrounding area after use. Put cutting powder in the specified container. Chips should not be mixed with combustibles.
- Do not leave running machines unattended.
2-3-3 Precautions for Laser Equipment
International standards for the manufacture and use of laser products are specified by IEC 60825-1 and in Japan safety standards conforming to this are found in JIS C 6802.- Place the laser device in as isolated a room or area whenever possible.
- Avoid installing laser devices with the light beam path at eye level as much as possible.
- Ensure that the laser beam terminates at the end of its effective optical path using an absorber or the like.
- Wear safety glasses and do not look directly at the laser beam.
- Reduce exposure the skin as much as possible. Avoid clothing with chemical fibers.
- Shield the periphery of the device before operating a laser, and do not let anyone other than stakeholders enter.
- Notify surrounding people during laser operation.
- Prevent reflection during laser operation or scattering of light by mirrors, lenses, window materials, etc.
- When using an invisible laser beam device, display an appropriate warning.
2-4 Transporting Materials and Working in High Places
2-4-1 Handling Objects and Preventing Accidents during Transport
Common accidents when handling or transporting heavy objects include dropping the object on your feet and pinching your hands. It’s also extremely dangerous if someone helping carry an object trips or relaxes their grip. It’s essential that everyone helping be aware of the need to prevent accidents.2-4-2 Transport Work Safety
Transportation work includes equipment such as cranes, derricks and chain blocks, and work with transport vehicles. This type of work can often require more than one worker, and the damage caused by transport accidents can be great, so using clear work rules is important. Please do the work of heavy load carrying under the direction of the person responsible for that work order.- Make sure to organize the travel route and the installation site in advance.
- Arrange a sufficient number of people to lift the required weight and size.
- Workers should start working only after all the workers understand the transportation procedure.
- Lifting weight with your back bent can cause injury. Use legs to lift weight by bending knees.
- Always listen carefully while carrying things, and pay attention to other people and surrounding circumstances.
2-4-3 Work Requiring a License, Skills Training, and Special Education
For crane operation and rigging work, a license and qualification are required. Unlicensed or unqualified persons cannot do the following work:- Operation of mobile cranes with the lifting loads is 5 tons or more.
- Operation of mobile cranes the lifting loads is less than 1 ton.
- Driving of construction vehicles such as construction machinery (leveling,transportation, loading etc.) weighting 3t or more.
2-4-4 Working at High Elevations
When working in high places such as on stepladders / ladders / scaffolds / rooftops or verandas, the following points should be noted.- According to the Occupational Safety and Health Law, work to be carried out at 2m(meters) or more from the ground is considered high place work, and prevent falls such as handrails etc, and a safety belt are required.
- Even if the height is less than 2m, ladders, stepstools, etc. should be used properly after sufficient safety confirmation. Be sure that ladders are held up and supported by a second worker during use.
- Do not underestimate the height of a place. Even falling from a slight height may cause death.
- Make sure to review the site with a supervisor or an assistant multiple times.
- Pay attention to clothing, wear a safety belt / safety cap, etc, wear slip resistant shoes.
- Be very careful not to drop tools and equipment. Do not leave things on scaffolds.
- Do not walk under elevated work places.
- Place ladders against walls at an angle of 15°. Choose a strong foothold and avoid places where people can pass under. Ascend and descend on the same ladder, should be limited to one person.
2-5 High Pressure Gas / Liquefied Gas
2-5-1 Caution on Handling High Pressure Gas
High pressure gas refers to one with a gauge pressure of 1.0 MPa or more (compressed gas), liquid state with a gauge pressure of 0.2 MPa or more (liquefied gas), and the rules of handling are stipulated by the High Pressure Gas Safety Act. Accidents involving high-pressure containers often lead to serious accidents, so carefully handle cylinders under the guidance of those with sufficient knowledge.- Become familiar with the nature and handling methods for various gases.
- Do not allow gas to escape.
- If you sense danger, close the valve of the container if possible and evacuate immediately.
- In order to act promptly, the experimenter himself should be conscious of the direction for closing the valve at all times.
- Also the use of gas for other purposes is prohibited.
- Use dedicated equipment (e.g., regulators). In particular, oxygen gas may ignite when it comes in contact with oil, so use equipment dedicated to oxygen.
2-5-2 High Pressure Gas Containers (cylinders)
High pressure gas containers (cylinders) should have a stamp on the cylinder shoulder that describes its content. Below is an example of a cylinder engraving: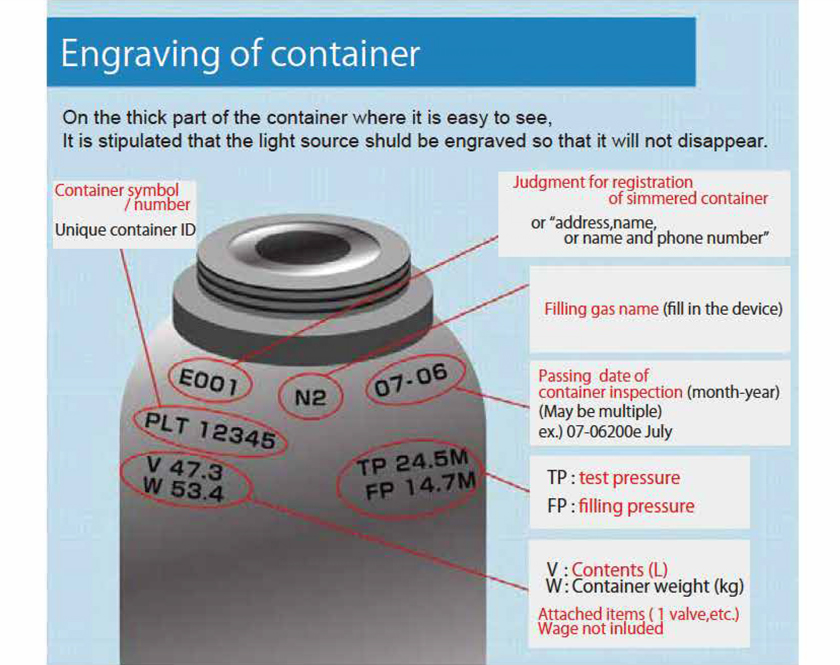
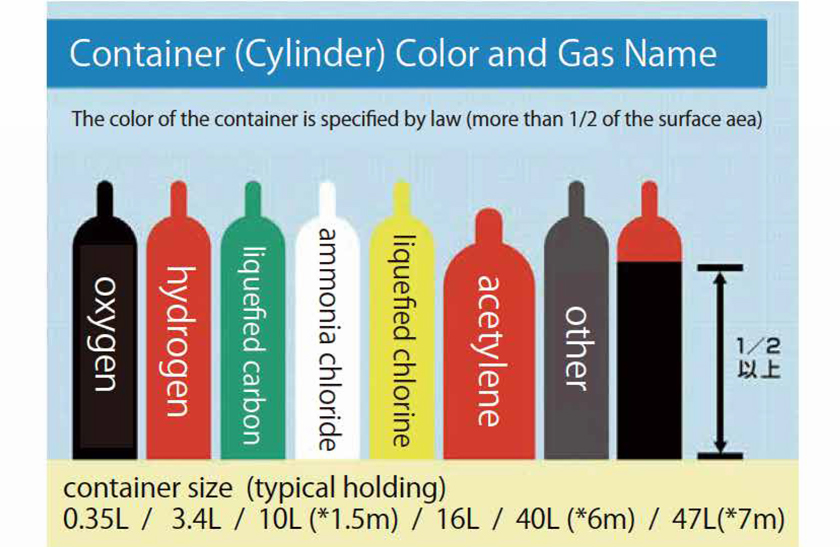
2-5-3 Pressurized Vessels (cylinders)--Precautions for Use
(1)Operation procedure:Secure the cylinder firmly to the wall and experiment base with chains or brackets. Connect the pressure regulator to the filling screw being careful not to over tighten or to connect threads at a wrong angle when connecting the fittings.Operation procedure.
(2) Pressure regulator
1) Filling screw screws are left-turning screws and others are right-turning screws for preventing danger (for example, so oxygen regulators cannot be connected to a hydrogen cylinder). The flammable gas has a left-turning screw and others have a right-turning screw (except helium, which is left, and methyl bromide and ammonia, which is right.). An oil-less screw is required for use with oxygen gas.
2) After confirming that the pressure adjustment handle is loose, gently open the valve of the cylinder (take more than 2 seconds to do it.). It is safer to operate the valve with the right hand.
3) Turn the pressure adjustment handle clockwise and adjust until the secondary pressure gauge reaches the desired pressure. If there is an outlet valve in the regulator open it. If necessary adjust the secondary pressure again. Always open and close the pressure adjustment handle carefully and not fully open. Use in a room with ventilation.
4) When use is completed, close the pressure regulator and container valve tightly in reverse order.
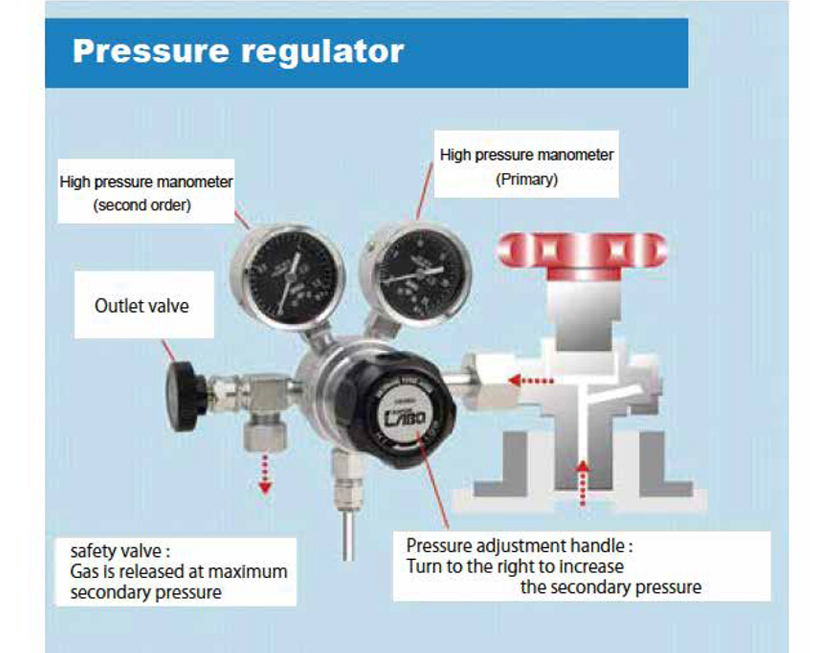
After using most of the gas, deliver used cylinders to the gas vendor leaving an approximate residual pressure of about 1 MPa. Do not leave cylinders completely empty. Pay attention to the primary pressure, and stop using it at a certain pressure or lower. The reason is that atmospheric contamination and backflow from the equipment, corrosion of the container, and a decrease in purity of gas can result in an explosion of flammable gas. Also, the transfer of gas from one cylinder to anther is absolutely forbidden.
(4) Storage and transport:
Avoid direct sunlight, be sure to secure cylinders to a wall or a laboratory bench with a chain in a place of 40°C or less. Cover all moving parts tightly with protective caps and carry carefully so as not to loosen the caps while on the cart. It is dangerous to roll cylinders on the bottom rim or to carry by hand.
2-5-4 Precautions for Flammable Gas, Oxygen, Toxic Gas, Asphyxiation Gas
- Flammable gas / toxic gas cylinders are to be installed in a room's cylinder cabinet with gas alarm sensors, water spray nozzles, and forced exhaust duct is equipment are stored in cabinets.
- Do not use fire or place combustible materials within 5 meters (m) of equipment that uses flammable gas (hydrogen, hydrocarbons, etc.), nitrogen trifluoride or oxygen.
- Oxygen is to be used only after removing combustible substances such as petroleum, fats and oils from appliances. For pressure regulators etc. which require oxygen, do not use flammable packing for connecting parts.
- To avoid inhaling toxic gas, handle in a local exhaust ventilation system.
- Exhaust gases outdoors, and render toxic exhaust gas harmless with alkaline absorbent filters etc.
- At the Toyosu Campus, when the pressure of gas (hydrogen, nitrogen, oxygen, argon) used in centralized piping decreases, close all the valves of the centralized piping system and contact the central monitoring room. Since the flowmeter of the gas used in the centralized piping is in the laboratory, it is preferable to check the usage amount about once a week.
2-5-5 Low Temperature Liquefied Gas
(1)Low temperature liquefied gas- Because it is cryogenic, this type of gas can cause frostbite. Wear dry leather gloves, protective glasses, protective surface etc. You must use gloves that cannot stick to the skin and cause frostbite.
- When handling liquids always wear long pants and hard, non-absorbant shoes.
- When liquefied gas vaporizes, its volume increases, replacing air and posing danger of suffocation.
- Do not put liquefied gas in sealed containers. Always make an escape port for vaporized gas.
- The liquefied gas container must be handled carefully and gently, and stored in a well-ventilated place without direct sunlight.
(2) Handling precautions for liquid nitrogen
1) Handling precautions
- When liquid nitrogen is used in a closed space, ventilate adequately so as not to deplete with oxygen in the space. Make sure that the closed place is visible from the outside and do the work with two or more people.
- Be sure to cover open type containers. In closed type containers, the pressure increasing valve and the liquid takeoff valve are to be kept closed and the gas discharge valve is kept open.
- Liquid nitrogen storage containers should not be layed on their sides. Because it is vulnerable to shock, handle it gently.
- When a container contains only metallic liquid nitrogen. tape should be wrapped around the outer circumference of the bare glass dewar bottle to prevent cracking due to contact.
- If liquid nitrogen is stored for a long time in a wide-mouthed container, oxygen enters from the atmosphere and liquid oxygen may accumulate. Since oxygen ignites violently when it comes into contact with organic matter, pay attention to the handling of fire around liquid oxygen containers.
- Do not ride in the same elevator that is carrying gas cylinders.
2) Handling precautions for liquid helium
- Liquid helium will suddenly evaporate with a slight heat inflow from the outside.
- Liquid helium is contained in a insulated metal vacuum container. Be careful not to tip over when moving because its high center of gravity increases the risk of tipping over. In addition, the inner container is an extremely thin special metal container designed to minimize heat inflow from the outside. Furthermore, since it is almost suspended at the cervical part, it is easy to break, so be very careful to protect it from shocks.
- In experiments, it is advisable to attach a balloon made of rubber to the evaporated gas discharge port for evaporation monitoring. However, when air flows backward from the discharge port, it solidifies on the inside of the container (the neck portion of the container) and becomes clogged, so be careful.
- Seek direction from those familiar with transport before transferring liquid helium using a dedicated transfer tube.
- When keeping liquid in a liquid helium container, carefully check the opening and closing of the safety valve installed at the top of the container, and the cover of the liquid helium supply port, and secure the gas discharge port (micropore), etc.
2-6 Chemicals
2-6-1 Chemical Substance Management and Laws
Research and educational activities at universities use a large number of chemical substances, and their properties vary widely.Handling with inadequate knowledge of the chemicals used is extremely dangerous and have a significant risk (Accidents such as explosions and fires, health hazards due to exposure to harmful substances, environmental destruction due to discharge and leakage)
To reduce the risks of such chemicals, we are regulated by various laws (Fire Service Act, Poisonous and Deleterious Substances Control Act, Industrial Safety and Health Act, High Pressure Gas Control Act) and Ordinances (Tokyo Metropolitan Ordinance on Environmental Security and Saitama City Ordinance on Preservation of Living Environment), Responsible measures are required from acquisition to storage, use, and disposal.
Experimenters should understand the risks of chemical substances on a daily basis and strive to conduct safe research and education.
2-6-2 General Provisions
- Shibaura Institute of Technology "School corporation chemical substance management regulations" were enacted on March 21st 2017 for the proper use and management of chemical substances, etc. Chemicals of interest are substances subject to regulation by relevant laws and regulations
- Relevant laws include the Occupational Safety and Health Act, the Poisonous and Deleterious Substitute Control Law, Fire Service Law, High Pressure Gas Safety Act, and ordinances concerning the environment that ensures the health and safety of the citizens of Tokyo
- In the Shibaura Institute of Technology's chemical substance management system, under the president, a chemical substance management officer is appointed for each campus and the person responsible for using chemical substances (faculty of the laboratory) in order to ensure the proper management and storage of chemical substances.
- Always investigate to see if chemical substances acquired for the first time constitute a danger or hazard
- Before use, please verify the safety and nature of the chemical substance using the safety data sheet (SDS) to become familiar with precautions on handling these substances and legal compliance obligations.
- Toxic substances, deleterious substances, hazardous materials, specified chemical substances, etc. must, of course, be stored, but their usage records must also be strictly prepared. It is necessary to submit the usage records for the previous year at the beginning of the fiscal year. If you purchase, use or discard chemicals, remember to record these transactions. ※ For details of how to manage chemical substances at the Omiya Campus contact the Section of Campus Facility and General Affairs of Omiya. For the Toyosu Campus contact to Facilities section.
2-6-3 Storage of Chemicals
- Keep chemical substances in a safe container clearly displaying the name.
- Exercise caution with chemical shelf items, being careful not to cause accidents due to mixing.
- Take measures such as attaching partitions to keep chemical bottles from breaking when an earthquake occurs.
- Especially poisonous substances and deleterious may cause danger to life even in small quantities, so strict storage and control book management procedures should be carried out based on laws and regulations.
2-6-4 Cautions for Using Organic Solvents
- Most organic solvents must be handled in local exhaust ventilation systems (fume hoods).
- Since organic solvent impacts the human health, careful handling should be used and, when poisoning occurs, appropriate first aid measures taken.
2-6-5 Hazardous Materials
- "Hazardous materials" are defined by the Fire Service Law as having explosive properties, ignitability, water proofing ability, flammability, and related properties and can cause serious accidents and disasters, so it is necessary to pay close attention to management and handling.
- The storage location of hazardous materials varies according to the type and amount of hazardous materials.
- Since the Omiya campus and Toyosu campus store a large amount of hazardous materials, operation management is strict, and the amount that can be brought into a room at any one time is limited.
- In addition to the laboratories, the Omiya Campus has a hazardous materials warehouse beside Building No. 6, and the Toyosu Campus has a hazardous materials warehouse under the main staircase, both of which are shared by all the departments.
2-6-6 Common solvents
On the Toyosu Campus, four types of organic solvents (acetone, hexane, methanol, and ethanol) can be used as a common solvent. These common solvents are hazardous substances in the Class 4 Class I petroleum category (methanol is designated as a deleterious substance) but due to a low flash point, are kept in the hazardous materials warehouse under the big staircase. These common solvents can be used for free in each laboratory at the expense of the school corporation, but please use "strict observance" of the following matters when using them:.- When pumping a common solvent, write down the department, supervisor, name, date, time and amount to be pumped in the ledger, and record when opening each new can
- Pay close attention so as not to spill solvent while pumping it out
- For carrying a common solvent, use a metal solvents can or a polycarbonate container made of organic solvent resistant material. Do not use a glass container.
On the Omiya Campus, the following solvents are available as common solvents: acetone, ethyl acetate, hexane, methanol, ethanol and diethyl ether. Because diethyl ether has a low flash point, special attention should be paid to fire. In addition, ethyl acetate and methanol are designated as deleterious substances and must be handled in accordance with the law. All of these solvents are stored in the hazardous materials warehouse next to Building 6.
These common solvents can be used free of charge in each laboratory at the expense of the school corporation. The following procedures must be strictly adhered to.
- Do not use fire in the hazardous materials warehouse. Before we go into the hazardous materials warehouse, we need to touch on a static eliminator pad which removes static electricity from the human body.
- The hazardous materials warehouse must be locked at all times and its keys must be kept under strict control.
- Doing refills and dispensing materials in hazardous materials warehouses is prohibited.
- Acetone and ethanol are stored in half cans (9L), 3L bottles, and 500mL bottles, respectively; methanol is stored in half cans (9L), 3L bottles. Ethyl acetate, hexane are stored in half cans (9L). Diethyl ether is stored in 500mL bottles only. Take out a solvent of a size appropriate to the amount needed (do not bring more into the laboratory than needed.) .
- When a solvent is carried in or out of the warehouse, write the date, time, name and quantity of the solvent in the provided delivery book. Be sure to accurately state the quantity after it has been removed.
- When carrying out the shared solvent, it should be in a container made of an appropriate material and strength, and transported in such a way as to prevent the container from tipping over or colliding with something. Use only transport equipment or containers that have been designed for such transport (e.g., safe bottles, bottle carriers, carts with baskets, etc.)
- If a person finds a leak, overflow, splash, etc. of a shared solvent, he or she must use the provided safety kit to prevent leakage of hazardous materials. Take first-aid measures and immediately contact the Hazardous Materials Security Supervisor.
2-6-7 Transport of Chemicals
Extreme caution is required when transporting chemicals, waste liquids, etc., including the above common solvents.- Before transporting, confirm that the container lid is properly closed and that the container has not deteriorated
- When carrying degraded containers and glass containers by truck, put them on a cart after putting them in corrugated paper or a plastic case with packing materials
- At the Toyosu Campus use the cargo elevator
2-6-8 Chemical Management System : IASO R7
- Some laboratories in the College of Engineering and the College of Systems Engineering and Science use IASO R7,chemical management system, so can understand inventory quantity and chemical useage issues related to stored toxic substances and deleterious substances.
If you wish to use IASO R7, please contact the Toyosu Facilities Management Section or Section of Campus Facility and General Affairs of Omiya.
2-7 Biological field
2-7-1 Microbial Experiments
- The most important thing to note in microbiology experiments is that the microorganisms handled are invisible to the naked eye.
- In the laboratory, a wide variety of micro-organisms float in the air, falling bacteria are present on experiment tables, and a large number of microorganisms can adhere to the experimenter. Therefore, before actually handling microorganisms, it is necessary to learn theories and techniques about disinfection, sterilization, and aseptic operation.
- It goes without saying that eating and drinking in a laboratory that handles microorganisms is prohibited.
- For experiments, please investigate the characteristics of the microorganism to be used beforehand and handle it according to its characteristics. Especially careful attention must be paid to unidentified bacteria isolated from nature. When handling microorganisms, be careful not to contaminate hands, clothes, and the environment with the materials used. Be sure to sterilize cultures before discarding them.
- When handling viable bacteria, do not put culture media or test tubes into which bacteria have been placed into your pocket during experiments. There is a danger of contamination due to leakage and breakage. Be sure to inform the faculty in charge of experiments whenever injured by glassware, needles etc. that seem to have attached bacteria.
- When handling dangerous microorganisms such as pathogens, take necessary precautions according to the risk group classification (National Institute of Infectious Diseases Research Institute Pathogen Safety Management Regulations).
2-7-2 Animal Experiments
- From the viewpoint of science and animal welfare, the "Shibaura Institute of Animal Experiment Regulations" has established both an ① Animal experiment committee approval procedure for animal experiment plans, and ② The Rules Concerning the Protection and Management of Animals", and "Standards Relating to Reduction and Storage of Experimental Animals and Pain Relief".
- It is necessary to apply for approved for each experiment plan and to get approval.
- An experimental animal is defined as any mammal, bird, or reptile that is kept for use in an animal experiment or the like.
(1) In order to conduct animal experiments, it is necessary to receive education and training on the following items:
- Related laws and regulations, guidelines, regulations prescribed by the Shibaura Institute of Technology, etc.
- Basic matters concerning the keeping of laboratory animals.
- Matters concerning safety assurance and safety management.
- Other matters concerning the implementation of appropriate animal experiments.
(2) In conducting animal experiments, experiments must be properly implemented according to the animal welfare management law and animal care standards, based on the following animal experiment principles:
- Utilize alternative methods (to the extent that the purpose of scientific use can be achieved) as much as possible to substitute for the use of animals.
- To reduce the number of uses (to the extent that the purpose of scientific use can be achieved), efficient and appropriate use of laboratory animals should be made to minimize the number of animals used for experiments.
- Experiments must be properly implemented based on the reduction of pain (to the extent necessary for scientific use, as much as possible by a method that minimizes the distress of the animals as much as possible). In addition, during animal experiments, we must beware of the possibility of receiving wounds and diseases from animal bites and from zoonosis, etc.
(3) In facilities dealing with experimental animals, observe the following:
- Wear special white clothing, footwear, cap, mask, and gloves.
- Do not eat or store food etc inside the facility.
- Before carrying out experiments, try to master the necessary procedures. If you are not confident, do it under the guidance of well-qualified people (faculty etc.).
- Conduct experiments only in designated areas and report to the teacher when injured during experiments. Use of anesthesia drugs, fixation reagents, and solvents should be carefully managed and ventilated.
- Avoid contact with laboratory animals if you feel unwell.
(4) For the breeding of laboratory animals, observe the following:
- Keep records on your entry into and exit from the storage facility and keep it locked to prevent others from entering.
- When breeding, try to maintain a comfortable environment by feeding, watering, cleaning, changing bedding, etc. while taking into consideration the ecology and habits of laboratory animals.
- Be careful not to let the experimental animals escape when changing the bedding etc. Should an experimental animal escape, notify the supervising faculty promptly after applying measures to prevent it’s escape to other rooms. Follow instructions for handling experimental animals that escape.
- If abnormal animals or dead animals are found in the storage facility, contact the faculty.
(5) The treatment of animals used in experiments shall be as follows:
- Use a specialized supplier to dispose of laboratory animals. Keep animals frozen in storage until the processing day so that there will be no liquid leaks such as blood. Avoid mixing aluminum foil and unnecessary paper, and make sure not to wrap up the used needle, cutlery, etc. with the remains.
- Bloody waste, needles, such as injection needles, and dangerous small cutlery, such as knife replacement blades, etc. must be stored in a freezer dedicated to infectious waste.
2-7-3 Genetic Recombination Experiments
(1) What are Genetic Recombination experiments?
Such experiments involve:
- The development of DNA recombination technology incorporates of the use of recombination creatures including the cultivation of recombination plants, which could have a negative impact on non-recombination biodiversity, including cultivated plants and wild animals, that inhabit natural environments.
- As a result, internationally, the "Convention on Biological Diversity (Cartagena Protocol)" was concluded and, in Japan, the domestic "Law on securing biodiversity by regulation of the use of genetically modified organisms" (Cartagena law),was passed in 2004.
① Type1: Used without doing nonproliferation measures in a farm and a factory.
② Type2: Used with nonproliferation measures in a laboratory or biological cultures device.
(2) About diffusion prevention measures, assuming type 2 use:
- In order not to release the recombinant produced in the laboratory into the outside environment, the following statutes are applied:
① "Ministerial Ordinance specifies that diffusion prevention measures etc. be taken in the use of the second kind of genetically modified organisms related to R & D, etc." (2004'Ministry of Education, Culture, Sports, Science and Technology, Ministry of the Environment Ordinance).
➁ "Guidelines for Recombinant DNA Experiments at University etc." (1998'Ministry of Education,).
③ "Shibaura Institute of Technology Gene Recombination Experiment Implementation Regulations" - These rules define biohazard measures in recombinant DNA experiments based on knowledge of general biohazards posed by pathogens.
- Genetic recombination experiments require application for and approval of the experimental plan and the experimenter must have adequate knowledge of microorganisms and related experimental methods.
- In order to prevent diffusion to the outside world, the physical containment by laboratory facilities, equipment, operation method, etc. are classified into levels P1, P2, P3, and P4, depending on the degree of risk of the recombinant.
- Biological containment is divided into levels of B1, B2 depending on the viability of the recombinant in the external environment.
2-8 Experimental equipment
2-8-1 Fume Hood
Fume hoods are used in work and experiments involving chemical volatilization and generation of dust etc. to prevent workers' exposure and indoor air contamination. Although it is mandatory to use local exhaust equipment, etc. when using organic solvents or specified chemical substances under the Occupational Safety and Health Law, it is not limited to substances specified by law, but in order to prevent exposure of hazardous substances in general, please use correctly.- Be sure to check the operation of the exhaust fan before use and use it.
- To prevent accidents such as inhaling chemicals, close doors as much as possible.
- To prevent electric shock accidents, do not perform switch operations and plug and unplug the power plug with wet hands.
- When gas odor occurs, immediately close the main gas valve, open the windows and doors and ventilate the room adequately. Trying to turn exhaust fans and ventilators on and off will cause sparks from the switch and there is a danger of igniting or exploding the filled gas.
- When using the heat source in the fume hood, keep it as far as possible from the inner wall and observation door.
- Due to different chemical resistance depending on the type of chemicals used, the working surface should be properly covered depending on the reagent to be used.
- The fume hood must undergo a periodic voluntary inspection, once per year to confirm its condition, exhaust capability, etc. by regulation.
2-8-2 Electric Furnaces
Beware of fire, burns, electric shocks, explosions. Especially at 100 ~ 500 °C, the inside of the furnace will not turn red, so it is necessary to clearly indicate "in use" = "hot".- Keep the periphery of the furnace in order, not placing combustibles nearby.
- Do not heat the furnace to excessive temperature. Also, pay attention to abnormal odor etc. during use, and monitor the side of the furnace for high temperatures.
- In an unmanned state, attach a post-it note etc. in which users, work contents, contact information, etc. are written.
- Do not touch the high temperature part of the furnace body.
- Do not touch heated test specimens directly with your hand. When handling test specimens, wear safety shoes and wear gloves.
- Do not let high temperature samples taken out of the furnace touch moisture immediately after removal. Particularly when casting molten metal (molten metal) into a mold etc, always do without moisture. As moisture adheres, water vapor explosion may occur, so be careful.
- Never put combustible gas or liquid in an electric furnace.
- Do not install furnaces under sprinklers.
2-8-3 Centrifuges
- In order to prevent the contents from scattering, securely replace the lid after using it.
- Use the proper attached rotor or bucket to maintain acceptable speed.
- The weight balance of samples is symmetrical with respect to the rotation axis (If you do not balance it, it may cause vibration of the centrifuge and destruction of the equipment).
- Set tubes and buckets at symmetrical positions so that the rotor balances.
- While driving, do not open the lid, and do not give a shock to the machine body.
- Do not touch the rotor or rotating shaft until the rotation has completely stopped.
- Perform periodic voluntary inspections.
2-8-4 Incubators
- Do not put chemicals such as volatile, flammable and corrosive gases in the cabinet.
- Do not put metals, foreign matter or flammable materials that cause ignition in the incubator.
- Never put samples in a sealed container, because expanding gas due to vaporization can cause the container to explode.
- Be careful as a short-circuit may occur when spilling water etc. inside the storage container.
- The heater switch must be turned off by the user after completion of work.
- When using continuously for a long time, take measures against empty cooking and overheating.
2-9 Radiation
2-9-1 Impact of Radiation on the Human Body
Radiation has permeating, ionizing and exciting properties, and is widely used in research. On the other hand, because humans cannot feel radiation, there is a danger of radiation exposure unless there is sufficient knowledge of radiation safety handling.In order not to cause radiation accidents, it is important to have a basic understanding of the characteristics of radiation, the difference between radiation and radioactivity radiation detection and prevention methods.
There are a small amount of radiation that we receive from the earth, space, and food. This is called natural radiation, and there are several types such as cosmic rays. There are regional differences in the exposure dose of natural radiation, but the global average is about 2 mSv per year. In addition, we may receive artificial radiation from medical equipment.
The radiation dose limit for radiation workers is set at 100 mSv / 5 year and 50 mSv / year by the rule for prevention of ionizing radiation disorders. This is about 10 to 25 times the level of natural radiation.
Generally, the influence of radiation on the human body becomes dangerous as a result of its influence on atoms, molecules, cells, tissues, organs and individuals, and its impact may also affect offspring.
Radiation exposure is internal exposure when the radiation source is in the body, and external radiation is from the outside of the body. The way to prevent these exposures is to prevent "inhalation, ingestion, percutaneous invasion" in internal exposure. Three principles of "time, distance, shielding" are important for external exposure.
2-9-2 Radioisotopes and Radiation Generators
Experiments using radioactive isotopes are conducted within an isotope controlled area, and the experimenter is required to take a special medical examination prescribed by law as well as education and training. Also, during experiments, you should wear a radiation dosimeter to record the exposure level. Furthermore, observe the following main points:- Since radiation is invisible, confirm with a measuring instrument whether there is contamination by radioisotope before and after starting the experiment.
- After the experiment is over, exit after confirming that the body / white suit / gloves / slippers are not contaminated.
- Handle with a good understanding of the physical and chemical properties of the radioactive isotope to be used.
- Those with little work experience must refrain from working alone We keep the laboratory in order so as not to cause a pollution accident.
- Do not bring unnecessary items into the laboratory, always make contamination checks when bringing laboratory items out.
- In case of emergency such as a radiation accident, theft of radioactive isotope, earthquake, fire, etc, report immediately to the radiological handling chief.
2-9-3 X-ray Devices
X-rays emitted from an X-ray generator such as an X-ray diffractometer or a fluorescent X-ray analyzer also have a risk of radiation damage to the human body These uses are prescribed by the Occupational Safety and Health Law and the Ionizing Radiation Injury Prevention Regulation and can be handled only by those who are permitted to use X - ray equipment. X-rays are harmful to the human body and it is necessary to pay close attention when handling to avoid exposure.
- When using the equipment, familiarize yourself with the functions and mechanisms of the equipment, minimize radiation exposure by avoiding careless handling. When installing, moving, or changing equipment, it is necessary to notify in advance.
- In the X-ray generating apparatus in which only the inside of the apparatus is set as the controlled area, safety parts such as interlocks for preventing exposure are attached to each part of the apparatus, so there is little risk of X-ray exposure during normal use, Although it does not become an object, the user needs to know the mechanism in advance and to work very carefully. Of course, do not inadvertently remove or change any parts.
2-10 Unmanned Aerial Vehicles (drones)
The aeronautical law amendment defines no-fly zones for unmanned aerial vehicles (drones etc.). On the Omiya campus drones are prohibited without near the student dormitory and the Omiya playground. If you wish to experiment with a drone at SIT, follow the "Procedures for Implementing Experiments Using Unmanned Aircraft".- Both indoor and outdoor are prohibited in principle.
- Indoors unmanned aircraft are only allowed in limited places (Toyosu Techno Plaza,Toyosu Research Building and Omiya Gymnasium).
- Flights may be permitted if there are measures to prevent collisions or erroneous operation, such as indoor (in Toyosu Research Building/Omiya Gymnasium) or outdoor drone flights, but please consult with the Research Promotion Office/Facilities Division in advance.
- With regard to the inside of laboratories, flying under the direction of the academic supervisor.
2-11 Laboratory Waste
2-11-1 Waste classification and treatment
Waste is broadly classified into household waste generated from the daily lives of ordinary households and business waste generated from business activities. Business wastes are further classified into two categories: industrial wastes (20 types of wastes) as defined in Act on Waste Management and Public Cleansing, and general business wastes other than industrial wastes.
Among industrial wastes, those with properties that may cause explosive, toxic, infectious, or other damage to human health or the living environment are defined as specially controlled industrial wastes, and their disposal is subject to stricter regulations than ordinary wastes.All waste generated by the university is classified as industrial waste and must be disposed of properly according to the rules.
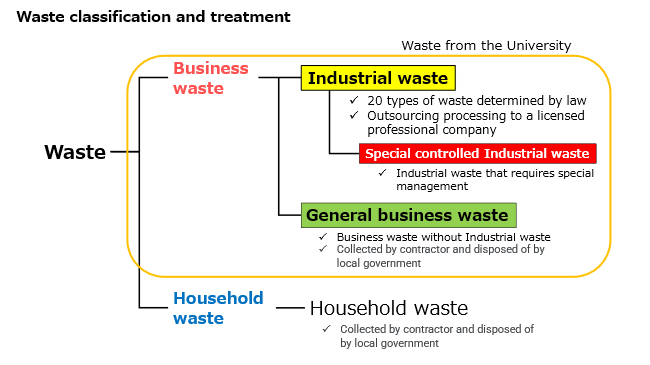
Business operators are required by law to dispose of business waste properly on their own responsibility. Therefore, if a business violates the law by illegally dumping or incinerating waste, it may be subject to penalties of up to five years in prison, a fine of up to 10 million yen, or both.
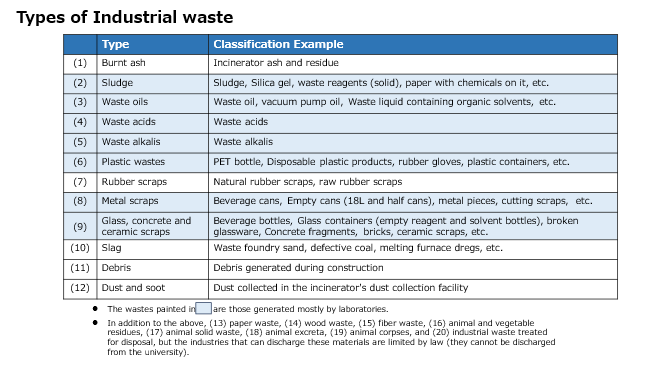
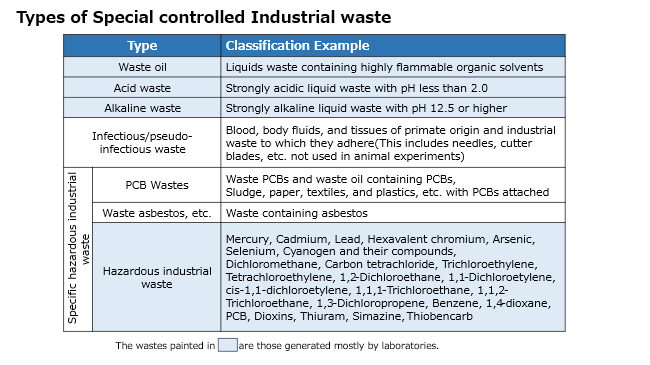
2-11-2 Experimental Waste
In addition to chemical substances and waste with attached substances, there are many other wastes in experiments and laboratories that cannot be disposed of without consultation, such as fungi being cultured, animals being observed, injection needles used, plastic centrifuge tubes, and substances containing mercury. Please consult with the Division of Campus Facility and General Affairs of Omiya or the Toyosu Campus Facilities Division before disposing of such waste. Also, if you drop a chemical bottle and break it, or spill a liquid waste, please consult and report the Division of Campus Facility and General Affairs of Omiya or the Toyosu Campus Facilities Division immediately.
Disposal of liquid waste from experiments is regulated by law and local ordinances because of the risk of ignition, water pollution, and soil contamination. Therefore, it is prohibited to dispose of reagents used in research and experiments, as well as containers, solid waste materials, and used reagent bottles with reagents attached, without permission. Among them, please dispose of liquid waste at the Toyosu Campus in accordance with the collection days held three times a year, and follow the procedures for disposal, such as submitting an application. At the Omiya Campus, please follow the separation rules, affix the lab liquid waste information sticker filled in according to the rules, and take it to the liquid waste warehouse (between Saito Memorial Hall and the gymnasium) for storage, distinguishing it according to the type of industrial waste. After pre-registration, you can bring in wastes from 6:00 to 22:00, Monday through Saturday.
The liquid waste should be stored in each room in a polyethylene tank provided by the university, tightly sealed, and clearly marked so that the contents, affiliation (name of laboratory or organization), and responsible person can be identified from the outside. Please check with the Division of Campus Facility and General Affairs of Omiya or the Toyosu Campus Facilities Division for specific details regarding these regulations and collection schedules.
For inquiries, please contact.
Omiya Campus:Division of Campus Facility and General Affairs of Omiya (Ext. 5000)
Toyosu Campus:Toyosu Campus Facilities Division (Ext. 7270)
2-11-3 Disposal at Toyosu Campus
Separation of experimental waste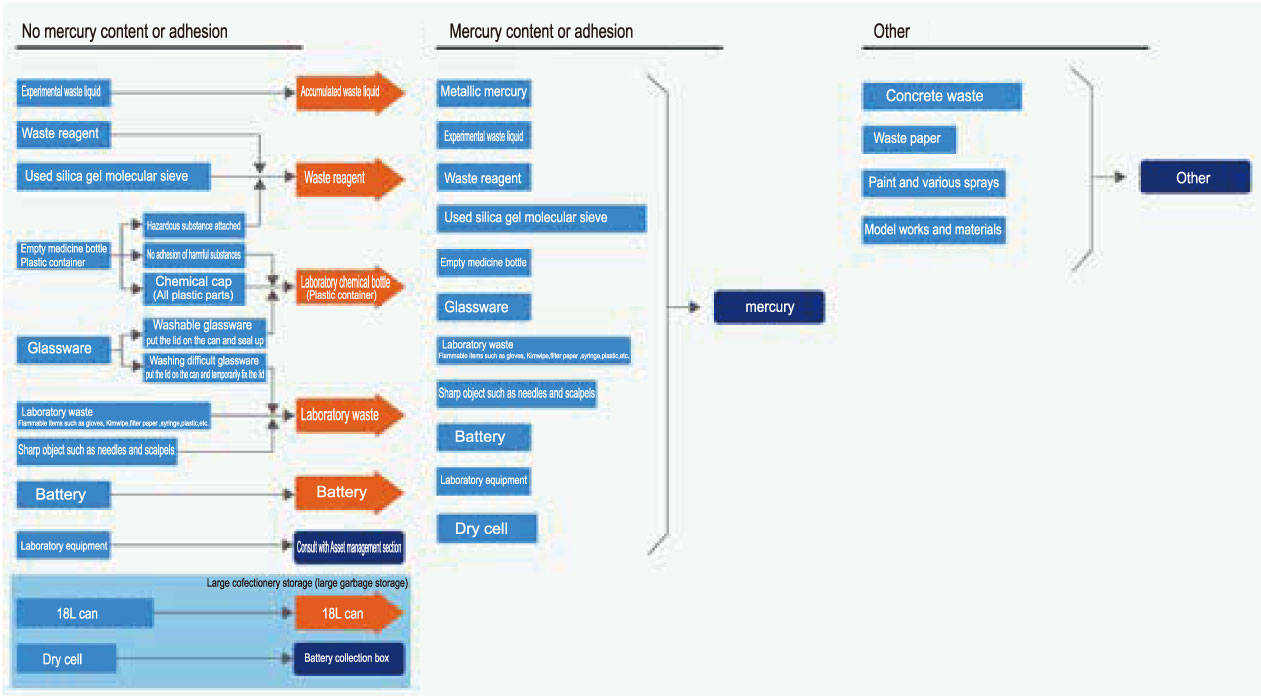
No mercury content or adhesion
Stagnant liquid waste
Waste reagent
Chemical bottles and plastic medicine containers for experiments
Experimental waste
Battery
Experimental equipment
18L can
Dry cell collection box
Items containing or adhering to mercury
Mercury
Other:
2-11-4 Disposal at Omiya Campus
Please separate and dispose of waste generated at the Omiya Campus in accordance with Saitama City's "Business Waste Disposal Guide.
The rules for waste separation are listed below.
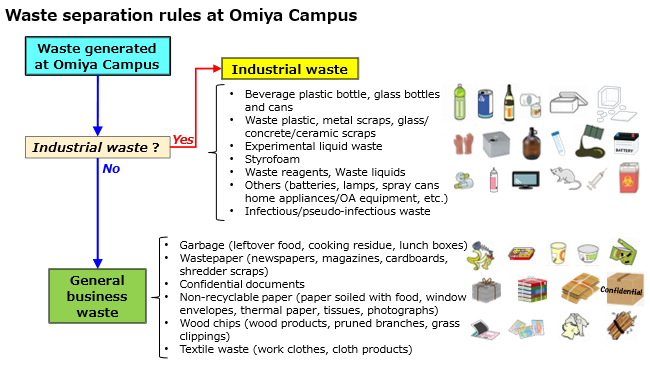
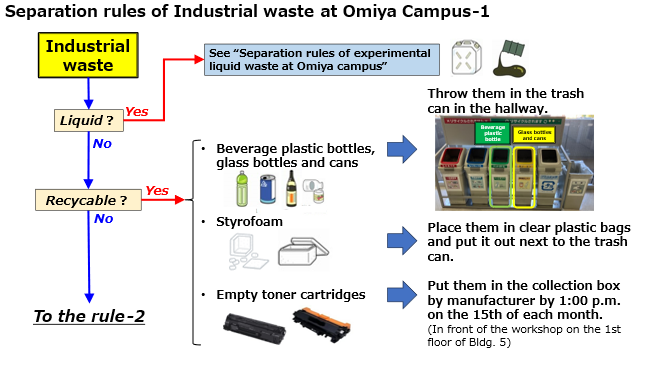
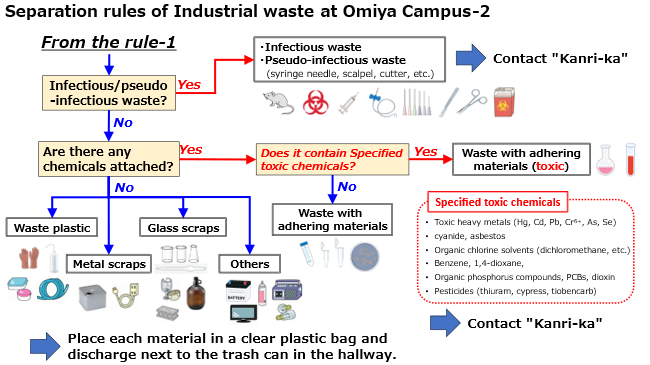
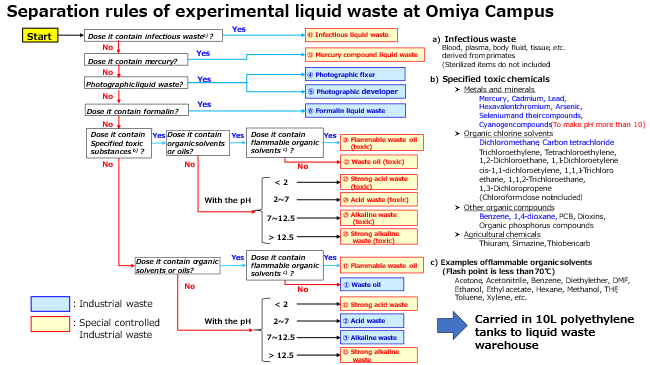
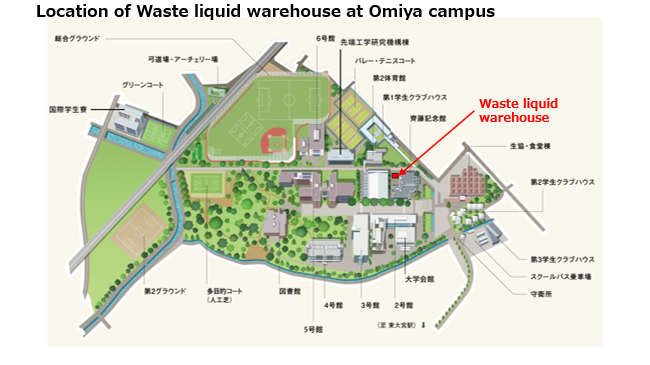
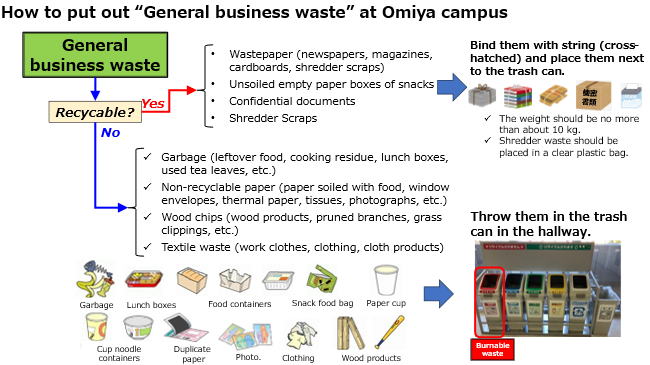